It is highly unlikely that an organization, whether it is in manufacturing, hospitality, or health care, can run without incident. However, the way the incidents are handled is what can help the organization remain competitive and achieve its business goals. When an incident happens, it needs to be investigated and effectively eliminated, which is where root cause analysis (RCA) comes into the picture.
There are many reasons why organizations should take Root Cause Analysis seriously. Organizations have used it for decades as part of their continuous improvement arsenal. But before we discuss how important RCA is when investigating an incident, let us quickly define what it is.
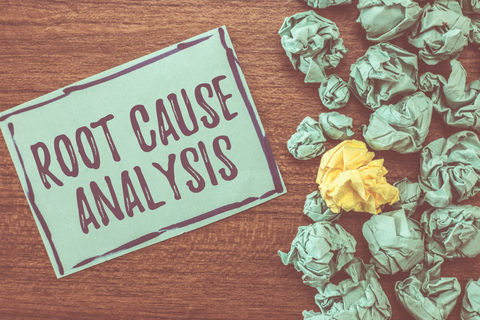
What is Root Cause Analysis and Why is it Important During Incident Investigation?
Root cause analysis can essentially be defined as a methodology that helps analyze an incident in order to identify the underlying (root) cause. Once the underlying cause has been identified, corrective steps are taken to eliminate it. So RCA is not just patchwork that takes care of incidents on a surface level.
When RCA is done properly, it means there is an extremely low (almost negligible) chance of the incident reoccurring in the future. This is perhaps one of the biggest reasons why RCA is important during an incident investigation.
Other Reasons Root Cause Analysis is Important
Besides helping an organization find a permanent solution for an incident, here are other reasons why organizations should conduct root cause analysis:
Helps Solve Similar Incidents
One of the end results of a root cause analysis is that an organization will come up with a systematic and logical approach to handling incidents. This approach can be adopted to help prevent similar incidents from occurring or reoccurring. That way, the workplace becomes a safer and more productive environment.
Products Get to Market Faster
When incidents occur, they slow down or completely stop production. While the incident is still in effect, it means that the organization’s ability to get products to market is significantly reduced. With the incident permanently dealt with, current and future delays are no longer an issue, which means products get to market faster and the organization makes money faster as well.
Reduces Costs
Defects are costly to rectify, especially when they occur in the later stages of the process. When defects are not caught and rectified, the defective products can make their way into the hands of customers. And since no one likes buying a defective product, it means these customers will be unwilling to buy from the organization again.
Improves Safety and Reliability
RCA makes products safer and more reliable. This means that consumers will have increased trust in the organization’s products. Moreover, with no incidents to worry about, current employees will feel much safer and highly-skilled workers will want to work for the organization.
Conclusion
As you can see, root cause analysis helps prevent incidents from reoccurring in the future by identifying and eliminating the underlying cause. Furthermore, it helps prevent similar problems from reoccurring, helps get products to market faster, reduces costs and increases the safety and reliability of products. Any organization that wants to stay ahead of the competition while being profitable will take RCA seriously.
No responses / comments so far.