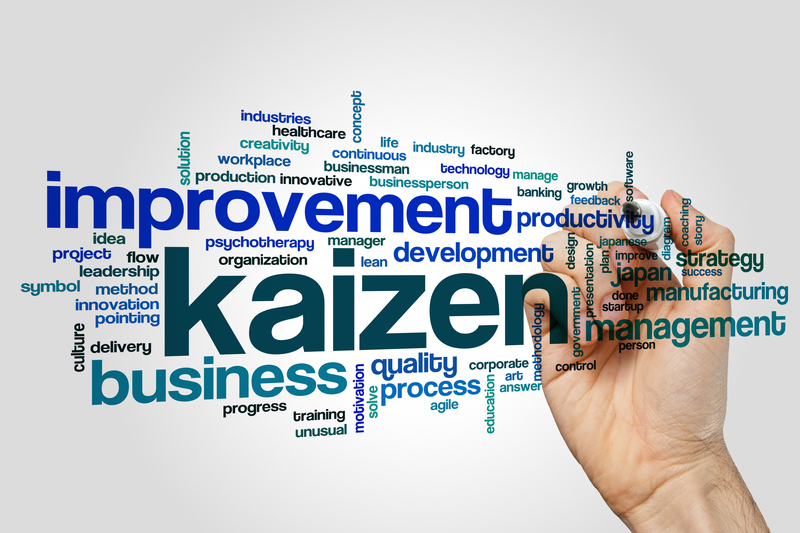
Kaizen is a philosophy that focuses on improvement in business activities, processes, and functions. It is a major force underlying lean production processes and also applies to business growth and lean software development.
The practice ultimately aims to reduce wastes and redundant processes. Kaizen involves every member of the business right from the CEO to the workers on the assembly line for optimized workflows.
Let’s see what Kaizen means, how it originated, and then explore the essential elements of this methodology.
What is Kaizen Methodology?
Kaizen goes beyond the traditional concepts of productivity improvement in business workspaces. It is all about increasing the human element, training the workforce to observe all processes they’re a part of and identify sources of improvement.
Kaizen thus mandates the participation of the whole business community — the entire workforce. Everyone, right from the management to those at the bottom of the business hierarchy are involved in Kaizen philosophy.
The methodology ultimately aims to produce goods and services without waste. This is done by improving processes and activities which are standardized.
Where Does Kaizen Come From?
The word Kaizen is Japanese in origin, being made of ‘Kai’, which means change, and ‘Zen’, which means good. Kaizen, therefore, means changing for the better. It doesn’t matter whether the change is big or small or if it’s constant — what’s important is that the change should contribute to betterment.
Kaizen is a widespread practice in Japan. The methodology was in use in the US before World War II, after which it entered Japan. Masaaki Imai is widely known for his work on the Kaizen principles and is considered by some as the father of Kaizen as we know it today.
Toyota is well-known to have used the Kaizen methodology to sustain business growth and achieve heights of success. The Toyota Production System employs Kaizen as a fundamental principle. The philosophy helps employees achieve superior productivity levels with rigorous practice and training.
What are Kaizen Principles?
The 5 principles of Kaizen are:
- Know Your Customer
- Let it Flow
- Go to Gemba
- Empower People
- Be Transparent
The three pillars of Kaizen include housekeeping, waste elimination, and standardization. At the core of the practice is continuous improvement.
Let’s now see some of the fundamental principles that lie at the heart of Kaizen.
- Continuous improvement: there’s no limit to improvement
- Don’t accept any assumption on the face of it
- Empower all employees to take decisions and contribute to the betterment of the business
- Make corrections if anything goes wrong
- Don’t strive for perfectionism and make small, iterative improvements along the way
- Avoid exorbitant expenses to save money to stay within your budgetary framework
- Ensure you never accept any excuses and get to the root of all problems, even if it takes time
- Question everything before you take any decision
- Look for problems and consider them opportunities to make processes better
- Check your progress from time to time and make improvements
Kaizen’s tools are actually the methods and techniques that can reduce waste in processes. Kaizen is thus a lean practice with a focus on waste elimination. Wastes constitute anything from defects and delays to extra-processing.
Summary
What does Kaizen mean in a nutshell? Kaizen implies continuous improvement for the better and engages employees at all levels. Conceptualized by Masaaki Imai, the practice is now used the world over. The methodology involves looking at problems as potential opportunities for improvement in an interactive, adaptive manner.
The approach aims to reduce waste and creates innovative solutions for problems rather than accepting the status quo. Team participation is encouraged in problem-solving rather than confining decision-making to the upper management levels. Ultimately, Kaizen is a humanizing approach for businesses that help in increase in production.
The philosophy is all about the reduction of wastes and simplification of processes to achieve higher quality levels and shorten time to market for higher customer satisfaction levels.
Comments are disabled for this post.