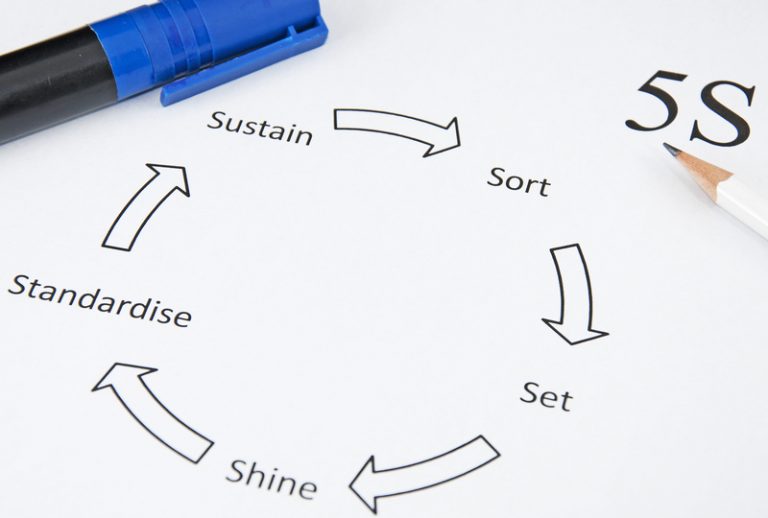
Many organizations struggle with making the workplace organized. An organized workplace is one where work gets done efficiently and effectively. It is also a place where employees have little to no worry about getting injured because it is so clean and organized. For this to happen, organizations need to put a system in place and 5S is one of the most tried and true methods in Lean thinking for achieving this.
5S (pronounced “five S”) is a Lean thinking tool that stands for Sort, Set, Shine, Standardise and Sustain. It is a system that strongly emphasizes putting everything in the right place. 5S has been used in many industries, from manufacturing to hospitality to healthcare. This is a system that can even be applied outside of the workplace to organize people’s homes, as well as lives.
Here is a brief explanation of what each S in the 5S means:
1. Sort
The first step in 5S is sort, and it involves taking an inventory of every item in the workplace. This includes all the tools, equipment, people and materials. Then, anything that is not useful in the workplace is removed to prevent it from getting in the way. Finally, the remaining items are grouped into two categories: frequently used and rarely used.
2. Set
Set is about arranging the remaining items in the most logical manner. That way, items can be picked up and returned where they belong easily, quickly and safely. If people are constantly having to look or walk across the workplace to find an item they need, it can lead to waste. Setting everything in order helps to significantly reduce this waste.
3. Shine
Shine is about ensuring that the workplace is clean. When the workplace gets busy, it is bound to get messy as well. This means tools, equipment and materials need to be returned to their rightful place, while the work areas need to be swept and mopped and the surfaces need to be dusted and wiped down. Putting the tools and equipment away ensures their longevity while everything else creates a much safer working environment.
4.Standardize
Standardize is what sets 5S apart from regular cleaning and helps make sure that the organization and safety levels achieved stick. Basically, this step is where 5S sets the entire organization up for continuous improvement by taking all the procedures used thus far and making them routine.
5. Sustain
Once the procedures have been standardized, more work needs to be done to maintain them, which is where the last S, Sustain, comes in. In order to sustain the results, everyone needs to be involved for it to be ingrained into the organization’s culture. If the results are not sustained, all the organization and safety levels achieved will revert over time.
Conclusion
As you can see, 5S is an important system for keeping the workplace organized. It paves the way for employees to do quality work by enhancing productivity and safety in the workplace. Furthermore, it lays down the foundation for continuous improvement. This is why it is one of the most popular tools in Lean thinking.
Interested in learning more about Lean Six Sigma Online training
Learn more about our training and courses
No responses / comments so far.