This is Part 3 of the Deming Red Bead Experiment Video Tutorial.
But, before the tutorial, below is a biography of Dr. W. Edwards Deming (credit to the deming.org), the creator of the Red Bead Experiment.
Biography of Dr. W. Edwards Deming
William Edwards Deming was born in Sioux City, Iowa on 14 October 1900 to William Albert Deming and Pluma Irene Edwards.
As an adult, he used the name W. Edwards Deming.
His brother, Robert Edwards was born on 11 May 1902; his sister, Elizabeth Marie, later Elizabeth Deming Hood was born on 21 January 1909.
The family lived at 121 Bluff Street in Sioux City. In 1904, they moved to the Edwards farm located in Polk City, between Ames and Des Moines. The farm was owned by Pluma’s father, Henry Coffin Edwards (Pluma’s mother, Elizabeth Grant, died when Pluma was young).
In an effort to encourage settlement in the West, the United States government granted parcels of land (usually 40 or 80 acres) to citizens who agreed to settle, farm or develop the land.
William Albert Deming filed on 40 acres in Camp Coulter, later named Powell, Wyoming. The family moved to Wyoming in 1907. They rented a house in Cody until they could build on their own land. William Albert learned that his parcel was poor, useless for farming.
Their first dwelling was a shelter, rectangular in shape (like a railroad box car), covered with tar paper, often referred to as a tar paper shack. Water was pumped from a well. There was little protection from the harsh weather. The family was often cold, hungry and in debt.
Eighty years later, on a visit to Powell, Dr. Deming learned that the 40 acres was still referred to as the Deming Addition.
Pluma Irene and William Albert Deming were well-educated and emphasized the importance of education to their children. Pluma had studied in San Francisco and was a musician. William Albert had studied mathematics and law. Young Ed Deming attended school in Powell and held odd jobs to help support the family.
In 1917, he enrolled in the University of Wyoming at Laramie. In 1921 he graduated with a B.S. in electrical engineering. In 1925, he received an M.S. from the University of Colorado and in 1928, a Ph.D. from Yale University. Both graduate degrees were in mathematics and mathematical physics.
Dr. Deming studied music theory, played several instruments and composed two masses, several canticles and an easily sung version of the Star Spangled Banner.
Dr. Deming married Agnes Bell in 1922 in Wyoming. Agnes and Ed had a daughter, Dorothy. Agnes died in 1930. Dr. Deming married Lola Elizabeth Shupe in 1932. They had two daughters, Diana and Linda. Dorothy died in 1984.
Dr. and Mrs. Deming lived in Washington, D. C. for the remainder of their lives in the house that they bought in 1936. With her family at her side, Mrs. Deming died on 25 June 1986. Dr. Deming, surrounded by his family, died at his home on 20 December 1993.
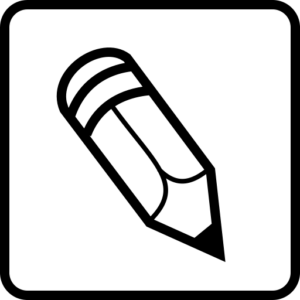
Video Transcript
[applause]
Male Speaker 1: Okay. On the other hand, we have Ken.
[laughter]
Ken, come on, come here. Now Ken, you’ve watched the other workers.
You see that it can be done. Don’t understand why you got 11 though. Clearly to see that you got 11 the most that anybody got, so I’m afraid I have to put you on probation. This company pays for performance, so you’re on probation.
We’re expecting your performance to improve. You’ve been trained, and you’ve seen your co-workers. So take your place. You’re on probation.
[laughter]
Male Speaker 2: We’d like to announce that management has an aide for the work force.
We realize that we have not been doing our part in trying to improve production, even though we have provided an excellent quality program and the appropriate slogans.
[laughter]
We did not provide you with a goal or an objective. You don’t know what it is you’re supposed to produce other then white beads.
So we have come up with an objective for you. That objective is three red beads per worker, per shift. We’re confident now that you understand the objective. The goal is, of management that you’ll be able to meet this objective. Remember, your jobs are contingent upon your performance.
Indeed the company…the continuation of the company is contingent upon your performance so please do your best to meet this goal.
Male Speaker 1: I’m very pleased. We now understand the goal is three or less red beads per worker.
We were keeping all these numbers, but we didn’t have a goal. Very important to have a goal. So the goal is three or less.
Visualize three, three, [laughter] very good. So we are now set in prime for our second day of work. Now with our fine experience and our goal of three, we should do great things today. Willing worker number one, come on forward, follow your procedure. Did we get out of order here?
Male Speaker 3: Can I ask any questions at this point?
Male Speaker 1: What kind of question do you have?
[pause]
I guess you don’t have a question…[laughter] so follow the procedure, and use the beads.
Male Speaker 3: The main thing was I couldn’t touch the beads?
Male Speaker 1: Right. You cannot. That’s why we have the paddle. Cannot touch the beads. Untouched by human hands. Cannot touch the beads. And you don’t need a pen, so put that away.
[laughter]
Male Speaker 3: Can I use a pen?
Male Speaker 1: There’s no need for a pen. There’s no pen in the procedure. Just go forward. You’ve been trained. We have the procedure. Yep, go forward.
No, you follow the procedure. There’s an extra copy right here.
[laughter]
And keep up our productivity. You’re delaying here.
Cover the holes and a 47 degree tilt, see? It works. No talking.
[laughter]
That keeps the productivity down. Stockholders just get paid.
Male Speaker 2: Ten, dismissed.
Male Speaker 1: Ten. You see Curt? All that questioning, your performance got worse.
[laughter]
Don’t ask questions. Willing worker number two, Marty. Ten yesterday. Let’s see here.
I’m expecting some fine improvement here. Just rotate it through up four inches, 47 degrees and on to QA. Following the procedure just beautifully.
Male Speaker 2: Seven, dismissed.
Male Speaker 1: Ah, our best performance yet. Yes, seven. Very good. Very good. You did three better that’s right. Seven. Okay, now comes Ed.
You’ve seen that it can be done. You can see that improvement but he still didn’t get three. Remember three. Three. Three red beads or less.
And a 47 degree tilt and on to QA. QA does count. Very important to have this independent count. It assures our quality count.
Male Speaker 2: Thirteen, dismissed.
Male Speaker 1: Thirteen. I don’t understand. Ed you were trouble from day one.
[laughter]
Now put the beads back in.
You were trouble from day one. Okay, Debbie with nine beads yesterday. Now just rotate it nice, and smoothly through.
If you just follow it along, all the beads will cover. You still let go…the other way.
Debbie: Oh dear.
[laughter]
Male Speaker 1: You are fired.
Female Speaker: You can’t fire me now! I quit!
Male Speaker 1: Boy, a hazard like that. You can’t quit.
[laughter]
Now we actually had somebody quit back at Savannah River, and we since written a procedure that says nobody quits.
Now I understand Tom Sheltnicks is in the audience and he was recommended to me as a replacement worker.
[applause]
Scratch off Debbie. Debbie no longer exists. We don’t acknowledge your existence now. And it is now Tom. But spell it for me please.
Tom: T-O-M.
Male Speaker 1: T-O-M. No H, just T-O-M. Now Tom, you’ve seen the on the job training, right?
Come on forward, it’s your turn, because of the failure of your predecessor. Here’s a copy of the procedure. And you understand the goal of three. Make sure the paddle is empty. There you go, very good, first time at it, I understand.
Ah this is very good, and up and rotate to 47 degrees. Oh, such a smooth operation onwards to QA.
[laughter]
Male Speaker 2: Seven, dismissed.
Male Speaker 1: Seven. I made a good choice here, did I not? Did you see my choice there, Mr. President?
Male Speaker 4: Well done.
[laughter]
Male Speaker 1: Ken, willing worker number five my probationary worker. Now you just saw was a brand new worker could do.
You too can be replaced.
[laughter]
Four inches and 47 degrees forward, and over to QA.
Male Speaker 2: Ten, dismissed.
Male Speaker 1: Ah, see, probationary programs work. We’re getting improvement albeit slow. I’m pleased, eleven to ten. Okay that’s good. Now where is Sid? My worker of the day from yesterday.
Up, and oh, that’s such a professional work there…
Male Speaker 2: Nine, dismissed.
Male Speaker 1: Well, you reward a person and it just goes to their head.
[laughter]
Okay. QA you can assist here…give me a total of the six people for day number and we can fill out our daily report.
Now I should state that we do performance appraisals here, and I suppose I didn’t tell you.
At the end of the third day, we do your performance appraisal, and it’s a completely fair method. See, we’re logging your performance.
Now what is the total for today please…17, 30, 37, 47, 56. Yeah, 56 right, 56.
Gee! Well we’re nothing if not consistent. Mr President, at the end of day number two, we made 56 defective products, 56 red beads.
Male Speaker 4: Well I acknowledge your consistency, but consistent poor performance it not really what we’re after.
[laughter]
Our customer is dissatisfied. Our management team is dissatisfied. I see that no worker has made three red beads. No worker has met our objective.
Clearly, management needs to provide some additional guidance.
And true to management form, we have come up with another program that we would like to implement. And I will have you explain this to the workers, but I think they may be familiar with it already. It is the star program.
Stop, think, act, and review. Would you please instruct the workers and explain to them how this will improve their performance?
Male Speaker 1: This is a very fine program. Because we just don’t believe you’re concentrating enough. You’ve got to concentrate and keep track of what is going on here. Just engage your brain and reach. One thing that’s motivational is reach on to your tippy toes.
Come on, everybody reach. Think about that. Reach.
[laughter]
My problem worker doesn’t reach… [laughter]
But stop, think, act, review. This will help you concentrate. Before you come up you stop, you think about your procedure, you act. And QA will review your performance. What could be easier?
This will help focus your attention. And remember the goal of three. And speaking of the goal of three…
Male Speaker 2: Speaking of the goal of three…
Male Speaker 1: Who gets to put the money for it?
Male Speaker 2: I got 10.
Male Speaker 1: I got the 20.
Male Speaker 2: All right, well…here, I’ll back half of it.
Male Speaker 1: So we believe in paid for performance at the White Bead Corporation. This is more than yesterday’s bonus in fact…we have a $30 bonus.
Kind of works well with three. The first worker to get the goal of three or less gets $30. Which we’ll put right here.
[recording ends abruptly]
Get instructions on how to conduct the Red Bead Experiment >>>
[contentblock id=16 img=gcb.png]
Comments are disabled for this post.